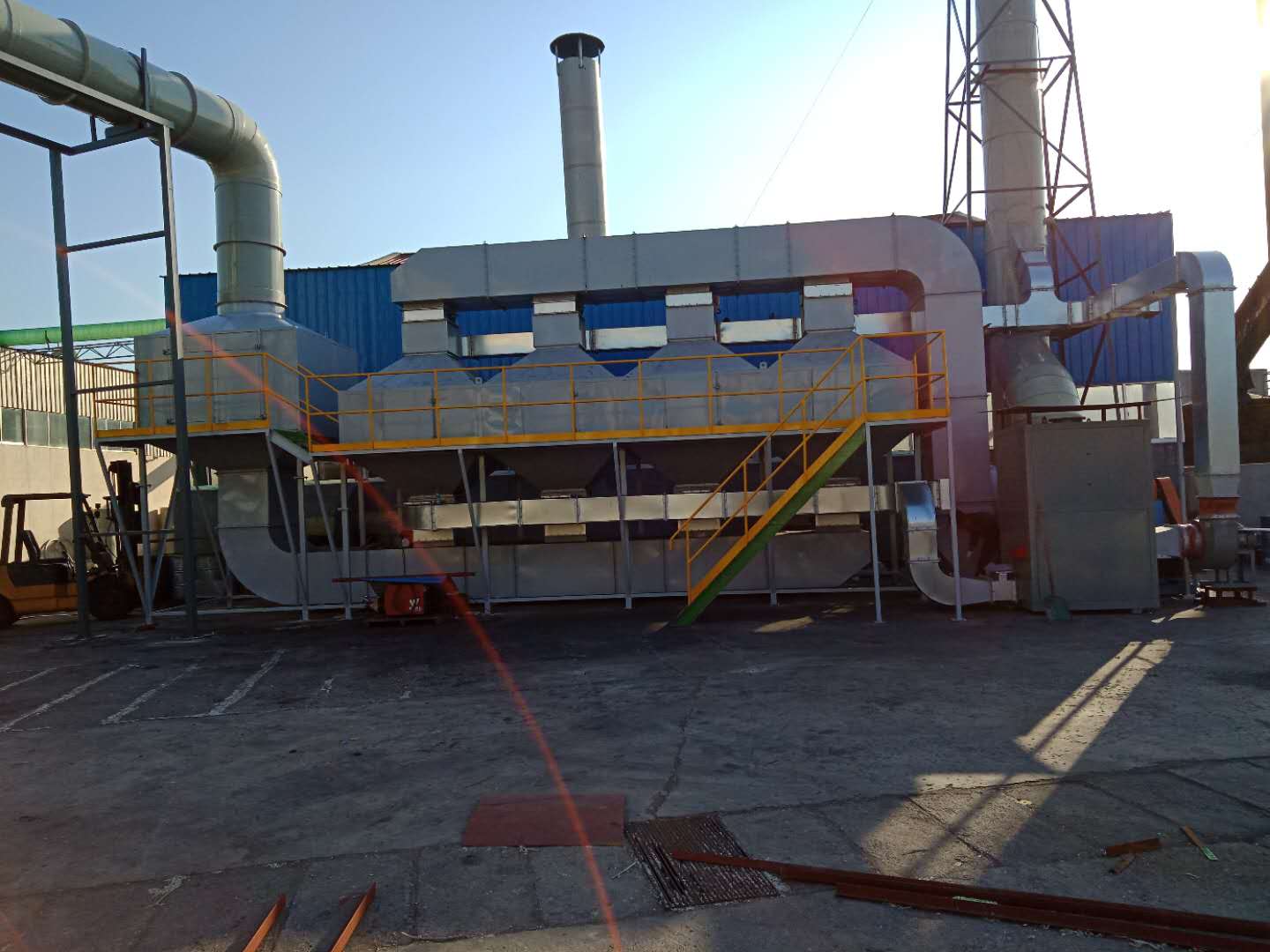
1、Design Principles
? Simple operation, stable operation, safe and reliable;
? Reasonable layout, low investment and low operating cost;
? More reliable treatment process and lower maintenance cost;
2、Process selection instructions
Organic waste gas treatment refers to the use of various technical measures to reduce the amount of organic solvents or exhaust gas purification through different ways to eliminate organic waste gas pollution. Organic waste gas pollution sources are widely distributed. To prevent pollution, in addition to reducing the amount of organic solvent to reduce the production of organic waste gas In addition to emissions, exhaust gas purification is currently a practical and feasible way of governance; commonly used methods include adsorption, absorption, combustion, condensation, and biological methods. When purifying methods are selected, low cost and consumption should be selected according to specific circumstances. The method with less energy and no secondary pollution, try our best to turn harm into profit, and fully recycle the components and waste heat;
According to the owner's requirements and our company's long-term experience in treating organic waste gas, activated carbon is used to adsorb and treat the organic waste gas. After the activated carbon is saturated, it is desorbed by catalytic combustion.
The exhaust gas from the spray booth contains a certain amount of paint mist, which is a viscous substance, so pretreatment must be performed before the exhaust gas enters the activated carbon adsorption device. Otherwise, the exhaust gas will cause unnecessary troubles and even invalidate the activated carbon because of the exhaust gas The sticky particles in the susceptible to "block" activated carbon.
3、Process flow
80000m3/hUsing four suction and one removal process;
Activated carbon adsorption (adsorption of organic waste gas) + catalytic purification (activated carbon regeneration) + exhaust system;
4、Process description
The process flow of the organic waste gas treatment project mainly includes three parts: the adsorption gas process, the desorption gas process, and the control system.
Adsorption gas process: The organic waste gas to be treated is led out of the air pipe and enters the activated carbon adsorption bed. After the gas enters the adsorption bed, the organic matter in the gas is adsorbed by the activated carbon and adheres to the surface of the activated carbon, thereby purifying the gas. The purified gas Then discharge to the atmosphere through the fan.
Desorption gas flow: When the adsorption bed is saturated with adsorption, stop the main fan; close the inlet and outlet valves of the adsorption box. Start the desorption fan to desorb the adsorption bed. The desorption gas first passes through the heat exchanger in the catalytic bed and then enters the preheater in the catalytic bed. Under the action of the electric heater, the gas temperature is increased to about 300℃ Then, through the catalyst, the organic material is burned under the action of the catalyst and is decomposed into CO2 and H2O, while releasing a lot of heat, the gas temperature is increased, and the high-temperature gas passes through the heat exchanger again to exchange heat with the incoming cold wind. Recover some heat. The gas from the heat exchanger is divided into two parts: one part is directly evacuated; the other part enters the adsorption bed to desorb the activated carbon. When the desorption temperature is too high, the supplementary cooling fan can be started to supplement the cooling, so that the temperature of the desorption gas is stabilized within a suitable range. When the temperature in the activated carbon adsorption bed exceeds the alarm value, the fire emergency automatic sprinkler system is automatically activated.
Control system: The control system controls the fan, preheater, temperature and electric valve in the system. When the system temperature reaches the predetermined catalytic temperature, the system automatically stops the heating of the preheater. When the temperature is insufficient, the system restarts the preheater to maintain the catalytic temperature in an appropriate range; when the temperature of the catalytic bed is too high , Open the supplementary cooling air valve to add fresh air to the catalytic bed system, which can effectively control the temperature of the catalytic bed and prevent the temperature of the catalytic bed from being too high. In addition, there is a fire damper in the system, which can effectively prevent the flame from returning back. When the temperature is too high when the activated carbon adsorption bed is desorbed, the valve is automatically opened to use the main fan to cool down;
4. Introduction of Processing Equipment
1、Activated carbon adsorption device
The adsorption box is made of carbon steel, coated with paint, equipped with a certain amount of activated carbon inside, and equipped with a high-temperature detection device. When the exhaust gas containing organic matter passes through the activated carbon adsorption layer (neatly stacked) through the action of the fan, the organic substance is unique to the activated carbon The force is trapped inside and the clean gas is discharged; after a period of time, when the activated carbon reaches saturation, the adsorption is stopped, and the organic matter has been concentrated in the activated carbon;
u The inner and outer walls of the adsorption box are made of Q235 t=2mm steel plate, the exterior is continuously welded, without bubbles, slag inclusions, etc., the overall appearance is beautiful;
u Internal circulation pipeline: the internal circulation pipeline is made of t=1.5mm Q235 iron plate, and the flanged bayonet connection is connected, the overall appearance is beautiful, the sealing performance is good, and the flange is connected by bolts;
u The main exhaust fan uses domestic high-quality products, the specific requirements are as follows:
2 The fan adopts 4-72/4-73 centrifugal fan, no temperature resistance requirement, driven by pulley;
2 The casing material is made of high-quality steel, and the impeller material is 16Mn;
2 The balance level of the fan is above 5.6; the noise is not more than 85dB (A);
2 The parameters such as fan air volume and wind pressure meet the design requirements and the performance is stable;
u Chimney: The chimney is made of t=3mm carbon steel plate; the chimney height is 15 meters;
2、Catalytic purification device
The catalytic purification device is equipped with a heating chamber, and the heating device is started to enter the internal circulation. When the hot gas source reaches the boiling point of the organic matter, the organic matter runs out of the activated carbon and enters the catalytic chamber to be catalytically decomposed into CO2 and H2O, and at the same time release energy, use the release When the energy that comes out enters the adsorption bed again, the heating device stops working completely, the organic waste gas maintains spontaneous combustion in the catalytic combustion chamber, and the exhaust gas is regenerated and circulated until the organic matter is completely separated from the inside of the activated carbon until the catalytic chamber is decomposed and the activated carbon is obtained. Regeneration, organic matter gets catalytic decomposition treatment;
Catalytic combustion: using catalyst as an intermediate to make organic gas into harmless water and carbon dioxide gas at lower temperature, namely:
The organic gas decomposed by the saturated activated carbon is sent to the purification device through the desorption fan, firstly through the dust removal flame arrester system, then into the heat exchanger, and then into the heating chamber, through the heating device, the gas reaches the combustion reaction temperature, Through the action of the catalytic bed, the organic gas is decomposed into carbon dioxide and water, and then enters the heat exchanger to exchange heat with the low-temperature gas, so that the temperature of the incoming gas rises to the reaction temperature. If the reaction temperature is not reached, the heating system will Compensation heating can be achieved through the automatic control system, so that it is completely burned, which saves energy, and the effective removal rate of exhaust gas reaches the standard emission, which meets the national emission standards;
The device is composed of a host, an induced draft fan and an electric control cabinet. The host of the purification device is composed of a heat exchanger, a catalytic bed, an electric heating element, a fire and dust suppressor, and an explosion-proof device. The fire and dust remover is located on the intake pipe and is explosion-proof The device is set on the top of the host, and its process flow diagram is as follows:
Features
u The precious metal palladium and platinum are plated on the honeycomb ceramic carrier as a catalyst, which has high purification efficiency, long catalyst life, smooth air flow and low resistance.
u
Complete safety facilities: equipped with fire protection dust collector, pressure relief port, over temperature alarm and other protection facilities.
u Power consumption: at the beginning of the work, preheat for 15 to 30 minutes at full power for heating, and only consume the fan power during normal work. When the exhaust gas concentration is low, automatic intermittent compensation heating.
Device advantages
u The equipment has advanced design principles, unique materials, stable performance, simple operation, safety and reliability, and no secondary pollution. The equipment occupies a small area, is light in weight, easy to load, and easy to replace.
u The catalytic combustor uses a ceramic honeycomb precious metal catalyst with low resistance, which can be operated normally with a low-pressure fan, which not only consumes less power but also has low noise.
u The air volume of the catalytic combustion device is one-tenth of the air volume of the waste gas source, and the heating power is maintained for about 1 hour, saving energy.
u The activated carbon bed that adsorbs organic waste gas can be desorbed and regenerated by the heat generated by the catalytic combustion treatment of the exhaust gas. The desorbed gas is sent to the catalytic combustion chamber for purification without additional energy, low operating cost, and good energy saving effect.
Material requirements for the entire device
u The external frame of the equipment is made of Q235 t=3mm carbon steel plate, the exterior is attached with paint, and the overall appearance is beautiful;
u The equipment panel is made of Q235 t=1.5mm carbon steel plate, the exterior is attached with paint, and the overall appearance is beautiful;
u The equipment insulation adopts 80kg/m3 rock wool insulation, the insulation thickness is 100mm, and the insulation effect is excellent;
u Catalytic combustion chamber is made of Q235 t=10mm carbon steel plate, the overall temperature resistance is good;
u The heat exchanger is made of Q235 t=1.0mm carbon steel plate, continuous welding outside, good internal sealing performance and high heat exchange efficiency;
u The equipment connection air pipe is made of Q235 t=1.2mm carbon steel plate, the exterior is continuously welded, and the overall appearance is beautiful;
u The desorption fan uses domestic high-quality products, the specific requirements are as follows:
2 The fan adopts YX9-35 centrifugal fan, which can be used under 250℃ for a long time, driven by the pulley;
2 The casing material is made of high-quality steel, the impeller material is 16Mn, and the bearings are NSK bearings;
2 The balance level of the fan is above 5.6; the noise is not more than 85dB (A);
2 The fan air volume, air pressure and other parameters meet the design requirements and the performance is stable;
u The external dimensions of the catalyst of the equipment are 100×100×40mm, high space velocity, good temperature resistance, and can work at 200-400℃ for a long time;
u The electric heating tube of the equipment is heated by stainless steel smooth tube, which is easy to clean and has good heating effect;
3. Technical performance and characteristics of the whole set of equipment
A. The equipment has advanced design principles, unique materials, stable performance, simple operation, safety and reliability, and no secondary pollution. The equipment covers a small area and is light in weight.
B. Using a new type of activated carbon adsorption material-honeycomb-shaped activated carbon, which has superior thermodynamic properties compared with granular (rod) shape, low resistance and low consumption, high adsorption rate, etc., which is very suitable for use under large air volume.
C. The catalytic combustion chamber uses a ceramic honeycomb precious metal catalyst, which has low resistance and can be operated normally with a low-pressure fan, which not only consumes less power but also has low noise.
D. The air volume of the catalytic combustion device is one-tenth of the air volume of the exhaust gas source. At the same time, the heating power is maintained for about 1 hour, saving energy.
E. The activated carbon bed that adsorbs organic waste gas can be desorbed and regenerated by the heat generated by the catalytic combustion treatment of the exhaust gas. The desorbed gas is sent to the catalytic combustion chamber for purification without additional energy, the operating cost is low, and the energy saving effect is remarkable.
4. Description of the main components of the whole set of equipment
Activated carbon adsorption system
? Activated carbon adsorption The core part of the whole device uses its own adsorption performance to purify organic waste gas;
? Adsorption fan adopts rear draft type to make the device work under negative pressure.
? Over-temperature alarm system to ensure the safe operation of the entire system of activated carbon during the desorption process;
? Thermocouple uses stainless steel protection tube to measure the temperature of carbon layer during desorption;
? Wind direction regulating valve adopts electric valve, electric actuator is of high quality brand;
? Control system The whole system adopts PLC control, which is safe and reliable;
Catalytic purification device desorption system
? The flame arrester is composed of a special multi-layer metal mesh, which can prevent the flame from passing and filter out larger particles (dirt) in the gas. It is one of the safety devices of this purification device.
? Heat Exchanger The heat exchange structure of plate type, its function is to use the heat released by the catalytic reaction to heat the imported exhaust gas, improve the utilization rate of heat energy, and reduce the heating power.
? Preheating chamber The exhaust gas preheated by the heater and the heat exchanger increases the intake air temperature to achieve the catalytic reaction conditions.
? Thermocouple uses stainless steel protection tube to measure the heating temperature and purification temperature of the intake air.
? Catalytic bed is composed of multi-layer honeycomb catalyst, which is the core of the device.
? Explosion-proof device is the pressure relief method of the diaphragm. When the equipment runs abnormally, the pressure can be cracked in time to prevent accidents.
? The desorption fan adopts the rear draft type to make the device work under negative pressure.
5. Safety measures of the whole set of equipment
? Fire retardant dust catcher A fire retardant dust catcher is installed in front of the catalytic purification device. One is used to clean the large particles in the air inlet, and the other is to prevent the flame from passing and cut off the danger between the production line and the processing equipment.
? Pressure relief port is a diaphragm pressure relief method. When the equipment runs abnormally, the pressure relief can be cracked in time to prevent accidents.
? Temperature over-temperature alarm There is a temperature over-temperature alarm inside the catalytic purification device. The safe temperature is set during the trial operation of the equipment. When the equipment is over-temperature, it will automatically open the fresh air valve to close the electric heating to dilute the intake air temperature to ensure Safe operation of equipment;
? Control system The whole set of equipment is controlled by PLC, with high degree of automation, safety and reliability;
? PID adjustment of valves Automatic adjustment between valves to control safe intake air temperature;
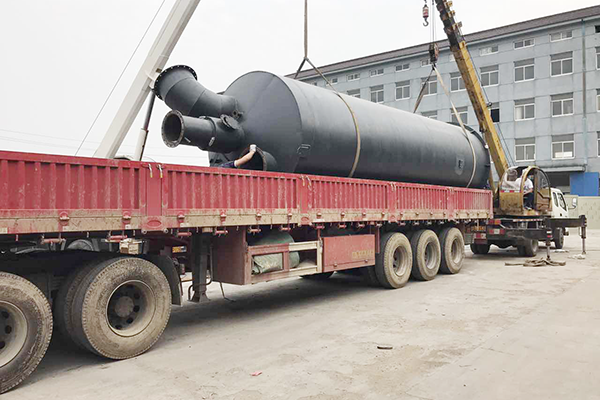
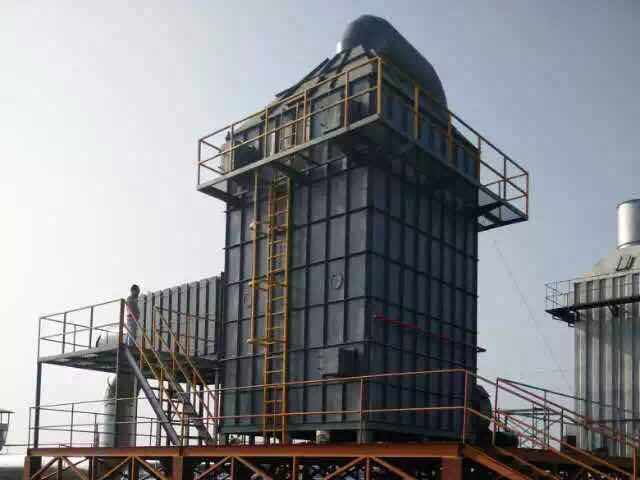
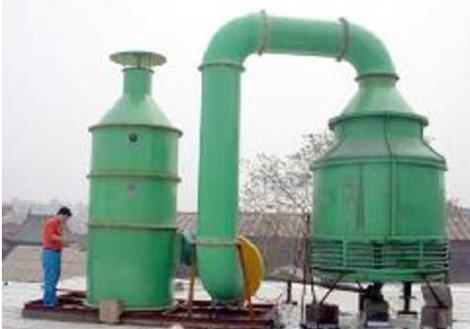
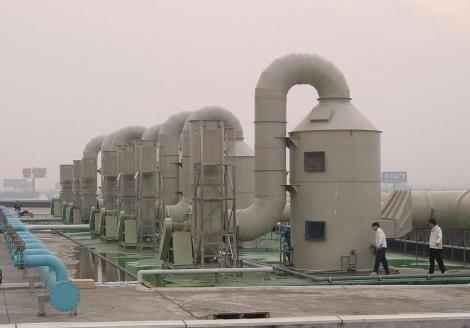